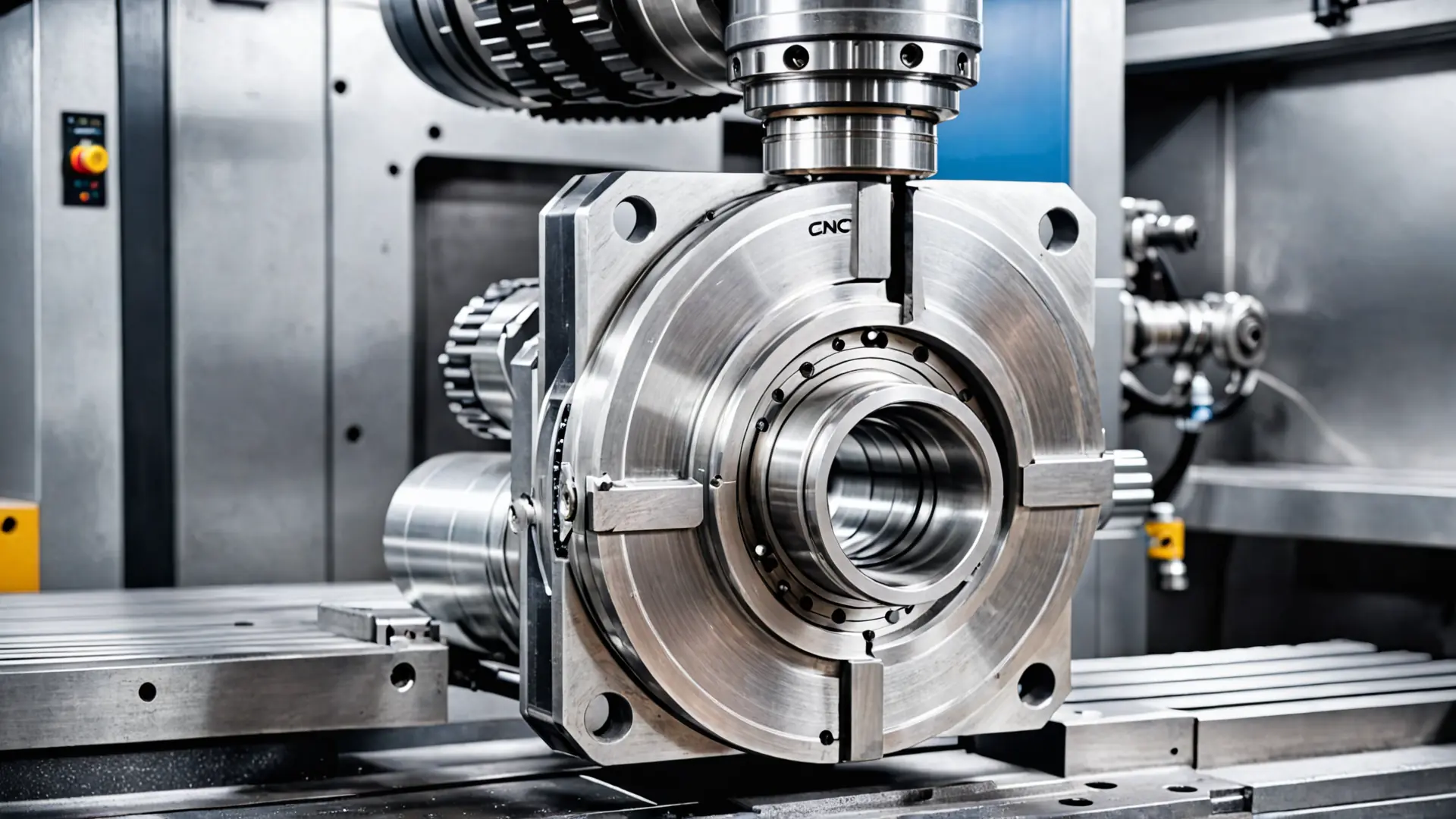
W dobie zaawansowanych wymagań jakościowych współczesne zakłady produkcyjne nie mogą pozwolić sobie na przeciętność – każde mikroskopijne odchylenie to ryzyko strat, reklamacji i utraty konkurencyjności. W tym kontekście modernizacja maszyn CNC przestaje być jedynie opcją konserwacyjną – staje się fundamentem ciągłości produkcji oraz jej precyzji. Aktualizacja wyeksploatowanych elementów prowadzi nie tylko do wydłużenia cyklu życia obrabiarki, ale przede wszystkim do zwiększenia dokładności, której oczekują dzisiejsi odbiorcy. Jakie układy warto unowocześnić? W jaki sposób kalibracja, nowe systemy sterowania i współczesne rozwiązania mechaniczne przekładają się na wymierną poprawę geometrii wykonanych detali? Przyjrzyjmy się temu krok po kroku.
Z tego wpisu dowiesz się:
- Maszyny CNC – czym są i dlaczego wymagają modernizacji?
- Kalibracja i geometria maszyny – fundament dokładności obróbki
- Sterowanie CNC nowej generacji – większa precyzja, płynność i kontrola
- Mechanika maszyny – wpływ stanu technicznego na precyzję
- Narzędzia i oprawki – precyzja zaczyna się od końcówki wrzeciona
- Oprogramowanie – cyfrowy fundament dokładności
Maszyny CNC – czym są i dlaczego wymagają modernizacji?
Zanim przejdziemy do omówienia konkretnych działań modernizacyjnych, warto wyjaśnić, co to są maszyny CNC. To obrabiarki sterowane numerycznie, które realizują precyzyjne operacje obróbcze na podstawie wcześniej zaprogramowanych instrukcji. Dzięki zastosowaniu układów sterowania komputerowego możliwe jest odwzorowanie skomplikowanych kształtów z wysoką powtarzalnością i minimalnym marginesem błędu.
Wraz z upływem czasu nawet najbardziej zaawansowane maszyny CNC zaczynają tracić swoją pierwotną dokładność – głównie z powodu zużycia komponentów mechanicznych oraz przestarzałego oprogramowania. Dlatego właśnie modernizacja obrabiarek staje się nieodzownym krokiem w utrzymaniu precyzji i stabilności procesu obróbki.
Kalibracja i geometria maszyny – fundament dokładności obróbki
Nawet najwyższej klasy maszyna CNC z czasem traci precyzję – nie z winy konstrukcji, lecz przez naturalne zużycie mechaniczne. Wydłużony czas pracy, zmienne obciążenia oraz mikrowibracje prowadzą do rozkalibrowania całego układu geometrycznego. Aby utrzymać spójność wymiarową detali, niezbędne jest wdrożenie systematycznych działań modernizacyjnych.
Dlaczego kalibracja jest nieodzowna?
- Zużycie prowadnic i mechaniki liniowej powoduje przesunięcia, które skutkują błędami w pozycjonowaniu.
- Oś X, Y i Z musi być dokładnie ustawiona względem siebie – minimalne odchylenia mogą przełożyć się na duże nieprawidłowości w wymiarach finalnego elementu.
- Niedopasowanie kąta między osiami generuje błędy kształtu, zwłaszcza przy skomplikowanej interpolacji.
Elementy, które warto objąć modernizacją:
- punkty podparcia konstrukcji – ich wzmocnienie poprawia sztywność oraz redukuje mikrodrgania,
- mechanizmy ustalające i blokujące osie – wymiana wyeksploatowanych komponentów przywraca stabilność torów ruchu,
- systemy pomiarowe geometrii – wprowadzenie laserowych analizatorów czy czujników osi umożliwia szybką diagnozę oraz precyzyjną korektę ustawień urządzenia.
Zmodernizowana maszyna, o poprawionej geometrii i stabilnej strukturze, zapewnia nie tylko lepszą jakość wykonania, ale też większą przewidywalność procesu – co staje się istotne przy produkcji seryjnej.
Sterowanie CNC nowej generacji – większa precyzja, płynność i kontrola
Układ sterowania jest jak mózg dla każdej maszyny CNC. Starsze jednostki, choć nadal sprawne, często nie nadążają za dzisiejszymi standardami przemysłowymi. Ich ograniczenia ujawniają się w momentach, gdy wymagane są błyskawiczne reakcje, perfekcyjna interpolacja lub integracja z nowoczesnym środowiskiem projektowym.
Dlaczego warto zmodernizować układ sterujący?
- Zwiększenie płynności ruchów – nowe sterowniki obsługują bardziej zaawansowane algorytmy interpolacji, co przekłada się na łagodniejsze przejścia między punktami i dokładniejsze kontury.
- Skrócenie czasu reakcji – nowoczesna elektronika eliminuje opóźnienia, które w starszych układach mogły prowadzić do błędów przy obróbce dynamicznej.
- Zgodność z aktualnym oprogramowaniem CAD/CAM – co umożliwia szybsze generowanie ścieżek narzędzi i minimalizuje ryzyko błędów związanych z konwersją danych.
Co należy usprawnić w systemach?
- Korekcja w czasie rzeczywistym – nowe sterowniki pozwalają na automatyczne wprowadzanie poprawek pozycji narzędzia w trakcie pracy.
- Kompensacja błędów termicznych – istotna przy długotrwałej obróbce lub pracy w zmiennych warunkach temperaturowych.
- Monitorowanie stanu narzędzia oraz detalu – funkcje umożliwiające analizę parametrów podczas procesu, bez potrzeby jego zatrzymywania.
Wymiana przestarzałego sterowania to krok, który radykalnie zwiększa możliwości maszyny, ale również operatora – nie tylko w zakresie precyzji, lecz także elastyczności w realizacji coraz bardziej złożonych projektów.
Mechanika maszyny – wpływ stanu technicznego na precyzję
Precyzja obróbki nie wynika wyłącznie z geometrii czy oprogramowania – to również kwestia kondycji elementów mechanicznych. Chociaż układy sterowania są niezwykle ważne, to właśnie części robocze decydują o tym, czy zadana trajektoria zostanie odtworzona z żądaną dokładnością.
Które elementy mechaniczne wpływają na jakość pozycjonowania?
- Prowadnice liniowe – odpowiadają za stabilność ruchu wzdłuż osi. Ich zużycie prowadzi do chwiejności, nieregularności toru oraz zwiększonych oporów.
- Śruby oraz nakrętki kulowe – przenoszą napęd z silnika na ruch liniowy. Luz osiowy lub wypracowanie gwintu przekładają się na błędy odwrotności.
- Łożyska liniowe – ich zużycie powoduje niejednolitą pracę poszczególnych osi oraz występowanie mikrodrgań.
- Pasy zębate i przekładnie – stosowane w napędach osi, mogą z czasem się rozciągać lub tracić sztywność.
- Sprzęgła elastyczne – tłumią drgania między silnikiem a śrubą napędową. Ich zużycie powoduje niedokładności przy gwałtownych zmianach kierunku.
- Podpory końcowe śrub – niedostateczne podparcie może skutkować ugięciami przy większych obciążeniach, co zaburza liniowość ruchu.
- Ramy i łoża maszynowe – wpływają na ogólną sztywność maszyny. Deformacje lub lokalne osłabienia konstrukcji prowadzą do przesunięć pod wpływem sił roboczych.
- Systemy kompensacji luzu – ich niesprawność zwiększa histerezę ruchu w punktach zwrotnych, co obniża dokładność przy powtarzalnych operacjach.
- Mechanizmy ustalające punkt zerowy – odpowiedzialne za precyzyjne pozycjonowanie detalu. Ich zużycie może powodować przesunięcia przy każdym nowym ustawieniu.
Jakie działania modernizacyjne warto rozważyć?
- Wymiana napędów na precyzyjniejsze serwonapędy – nowsze silniki oferują lepszą dynamikę, wyższą rozdzielczość enkoderów oraz efektywniejsze systemy kontroli zwrotnej.
- Modernizacja układów chłodzenia i smarowania – poprawne utrzymanie temperatury zapobiega mikroskopijnym deformacjom komponentów mechanicznych, co ma bezpośrednie przełożenie na stabilność wymiarową detali.
- Redukcja luzów strukturalnych – poprzez zastosowanie nowych rozwiązań podparć i kompensatorów, eliminowane są drgania oraz niepożądane przesunięcia podczas nagłych zmian prędkości.
Mechaniczna kondycja maszyny jest jak napięcie strun w precyzyjnym instrumencie – jeśli którykolwiek element odbiega od nominalnych parametrów, rezultat całego procesu może być niestabilny i trudny do powtórzenia. Dlatego też modernizacja obrabiarki wiąże się często ze ścisłym spasowaniem elementów roboczych, aby zachować jak najwyższą precyzję działania.
Narzędzia i oprawki – precyzja zaczyna się od końcówki wrzeciona
Narzędzia skrawające oraz systemy mocujące są jednym z kluczowych elementów w procesie obróbki CNC. To one decydują o jakości cięcia, precyzji kształtów i stabilności całego procesu. Właściwie dobrane oraz utrzymane narzędzia pozwalają na uzyskanie wysokiej jakości detali, bez konieczności przeprowadzania poprawek po obróbce.
Jakie problemy mogą wystąpić, gdy narzędzia są nieodpowiednie lub w złym stanie?
- Mikrowibracje, które zaburzają dokładność – jeśli narzędzie jest niewłaściwie zamocowane lub zużyte, jego drgania mogą prowadzić do uzyskania błędnych wymiarów.
- Zwiększone zużycie materiału – nieostre narzędzia wymagają większego nacisku na materiał, co skutkuje przegrzewaniem, a w efekcie mikroodkształceniami detalu.
- Zmniejszenie trwałości narzędzia – niewłaściwa geometria ostrza powoduje szybsze zużycie narzędzia, a tym samym obniżenie efektywności produkcji.
- Brak powtarzalności procesu – zużyte narzędzia powodują nieregularności, które mogą wpłynąć na zmienność wymiarów w serii produkcyjnej.
- Zwiększone tarcie – zużycie narzędzi prowadzi do wyższych temperatur w obrabianym materiale, co może wpłynąć na jakość powierzchni i kształt detalu.
Jakie działania pozwolą utrzymać narzędzia w doskonałej kondycji i zapewnić precyzyjność obróbki?
- Regularna kontrola stanu narzędzi – inspekcja zużycia narzędzi, szczególnie ostrzy, pozwala na wcześniejsze wykrycie problemów i ich szybszą wymianę, co minimalizuje ryzyko błędów.
- Optymalizacja parametrów skrawania – dostosowanie prędkości posuwu, prędkości obrotowej i głębokości skrawania do materiału czy rodzaju narzędzia pozwala na wydłużenie jego żywotności, a także poprawę efektywności obróbki.
- Inwestycja w nowoczesne systemy mocujące – systemy mocujące, takie jak oprawki z systemem amortyzacji, zmniejszają ryzyko bicia narzędzia.
- Używanie narzędzi wysokiej jakości – elementy o wysokiej trwałości, wykonane z materiałów odpornych na zużycie, znacząco poprawiają jakość obróbki i zmniejszają ryzyko awarii.
- Regularne konserwacja narzędzi – zapobiega ich nadmiernemu zużyciu, co przekłada się na utrzymanie stabilnej jakości pracy.
Oprogramowanie – cyfrowy fundament dokładności
Programy sterujące odgrywają dużą rolę w obrabiarkach sterowanych numerycznie. Nawet najlepsze maszyny nie będą w pełni wykorzystane bez zaawansowanych algorytmów sterujących, które umożliwiają precyzyjne zarządzanie procesami. Dlatego też modernizacja maszyn CNC wiąże się także z dbaniem o aktualizacje oprogramowania.
Jak oprogramowanie wpływa na dokładność?
Nowoczesne systemy sterowania umożliwiają precyzyjne zarządzanie trajektorią narzędzi, optymalizację parametrów skrawania oraz monitorowanie procesu w czasie rzeczywistym. Dzięki temu obróbka staje się bardziej płynna, dokładna, a także powtarzalna, co bezpośrednio przekłada się na efektywność produkcji. Integracja z systemami MES zapewnia szybkie wykrywanie anomalii, co pozwala na natychmiastową korekcję błędów i minimalizację ryzyka powstawania wadliwych elementów.
Modernizacje maszyn CNC powinny być przeprowadzane przez specjalistów z branży, ponieważ są one ważnym elementem strategii rozwoju współczesnych zakładów produkcyjnych. Inwestowanie w aktualizację podzespołów – od systemów sterowania, przez mechanikę maszyny, po narzędzia robocze – pozwala nie tylko poprawić dokładność obróbki, ale także zwiększyć efektywność i stabilność procesu produkcyjnego. Regularne modernizacje oraz aktualizacje oprogramowania zapewniają ciągły rozwój technologiczny, co pozwala na utrzymanie konkurencyjności w wymagającym środowisku przemysłowym. Warto więc traktować modernizację jako inwestycję w przyszłość, która przynosi wymierne korzyści zarówno w krótkim, jak i długim okresie.